HPQ Shatters Fumed Silica Tech With Reductions Of 93% CapEx, 90% Energy and 84% Greenhouse Gases
AGORACOM Small Cap CEO Interviews - Een podcast door AGORACOM
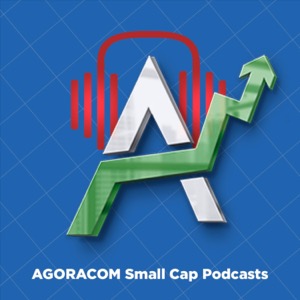
Categorieën:
HPQ Silicon is on the verge of disrupting the manufacturing process of Fumed Silica and becoming the sole provider capable of satisfying the strong demand for low carbon Fumed Silica products. How disruptive is the HPQ Silicon Process? Energy Consumption 90% Lower Greenhouse Gases 84-88% Lower Capital Costs 93% Lower Hydrogen Chloride Gas Complete Elimination GIANTS OF FUMED SILICA MARKET HAVE TAKEN NOTICE AND SIGNED NDAs More than just talk, the Fumed Silica industry has taken notice as evidenced by multiple NDAs with leading manufacturers immediately after HPQ announced the successful production of Fumed Silica samples through its proprietary Reactor technology. It's time for investors to take a closer look at the groundbreaking strides HPQ is making in reducing the carbon footprint, while also shattering the economics of the Fumed Silica industry. These multiple non-disclosure agreements with leading manufacturers in the Fumed Silica space attest to HPQ's remarkable achievements. But what exactly is Fumed Silica, and why is the industry buzzing about it? UNVEILING FUMED SILICA Fumed Silica, a versatile micro-powder, isn't just another industrial substance. Its potential to reshape numerous industries, from cosmetics and toothpaste to powdered foods, makes it a game-changer across personal care, pharmaceuticals, agriculture, adhesives, construction, batteries, and beyond. A MILESTONE IN GREEN ENGINEERING AND COMMERCIALIZATION PATHWAY The company has taken a significant step towards commercialization and is advancing with the pre-commissioning of a 50 tonnes per year (TPY) FSR Pilot Plant, signalling promising prospects. OPERATIONAL PILOT PLANT BY EARLY IN Q3 The pre-commissioning phase is progressing well, setting the stage for the pilot plant's operational launch in Q3. This milestone is pivotal as HPQ aims to transition from lab-scale production to commercial-grade outputs, addressing the high demand for eco-friendly fumed silica. The pilot plant will initially produce fumed silica with specific surface areas between 150 and 200 m²/g, eventually targeting over 300 m²/g for food and pharma applications. MULTIPLE COMMERCIAL PLANTS GLOBALLY The company is preparing for a future that could see the deployment of numerous 1,000-ton per year reactors to meet global demand. The local production model reduces transportation costs and environmental impact, further enhancing HPQ's competitive edge. WORDS FROM HPQ CEO Bernard Tourillon, President and CEO of HPQ Silicon and HPQ Silica Polvere, stated, "The materials produced will be sent to several potential clients under nondisclosure agreements for qualification. These potential clients, who have expressed keen interest in our material, could become strategic partners in our journey. We aim to negotiate offtake agreements for our low-carbon fumed silica material with them." The updated technical and economic study reveals remarkable cost efficiency and market potential: Capital Expenditure: Around US$10 per Kg of annual capacity, drastically lower than the traditional US$146 per Kg, reducing entry costs by about 93%. Energy Efficiency: Consuming 10-15 KWh per Kg of fumed silica, versus the conventional 100-120 KWh, marking a 90% reduction. Profit Margins: Revised EBITDA margins for fumed silica with 150 m²/g surface area range from 72% to 80%, significantly higher than the industry average of 20%. These figures underline the transformative potential of HPQ's technology, which not only slashes production costs but also enhances environmental sustainability.